Services
SOLAR FARM INSPECTION
SOLAR FARM INSPECTION
Drones In Solar Energy
Traditional solar field assessments consist of inspecting each panel with handheld thermal imagers to check for defective cells or cables. During this process, personnel have to manually keep track of the locations of anomalies to perform maintenance afterward. Because of the scale of most solar farms, this method of inspecting results in inefficient and imprecise data.
The integration of drone technology has completely improved the efficiency and accuracy of the inspection process. Thermal cameras, can survey large areas within a solar farm, collecting high-resolution infrared images during just a single flight.
The Benefits of Using Drones for Solar Inspections
Traditional solar field assessments inspect each panel with handheld thermal imagers to check for defective cells or cables. During this process, personnel has to manually keep track of the locations of anomalies to perform maintenance afterward. Because of the scale of most solar farms, this method of inspecting results in inefficient and imprecise data.
No. 1
%
Decrease in inspection costs
No.2
%
Accuracy in anomaly identification
No. 3
%
Reduction in inspection time
The Benefits of
Using Drones for Solar Inspections

Visual & Thermal Images
Aerial images provide a broader perspective of solar farms and allow maintenance teams to receive valuable information in real-time. When analyzing thermal images, it is easier to identify potential anomalies across cells, strings, or panels. Combining thermal and visual data helps you determine if the heat anomalies are caused by faults found physically on the panel, such as delamination, cracks, dust, or internal issues such as the inability to connect to a panel due to an inverter or cable failure.
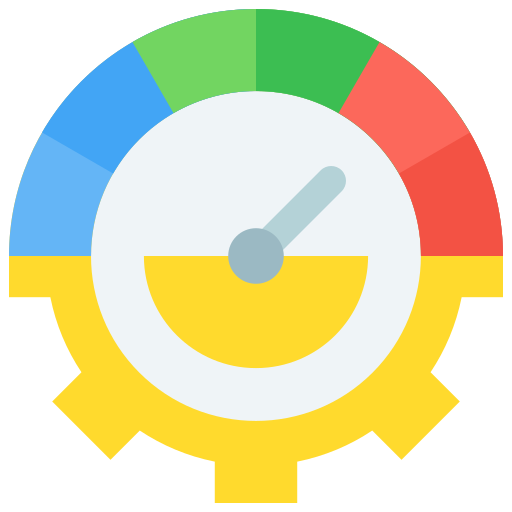
Output Efficiency
Early detection of faulty elements within a solar farm will help to prevent major output deficiencies. The faster and more accurately a maintenance team can detect possible defects, the quicker they can respond and prevent major system failures. Inspections and maintenance that are effectively conducted translate into protecting the interests of investors and ensuring that the the PV system is operating at its peak efficiency.

Detailed Reports
With use of thermal and visual images, the data is run into our industry leading software to detect all anomalies. These issues are then tagged, geo referenced, and reviewed for efficient remediation. Each defect from cell to string level is described with thermal and visual images for reference. Our reports also include an interactive map of your solar plant with the ability to easily share with other team members.
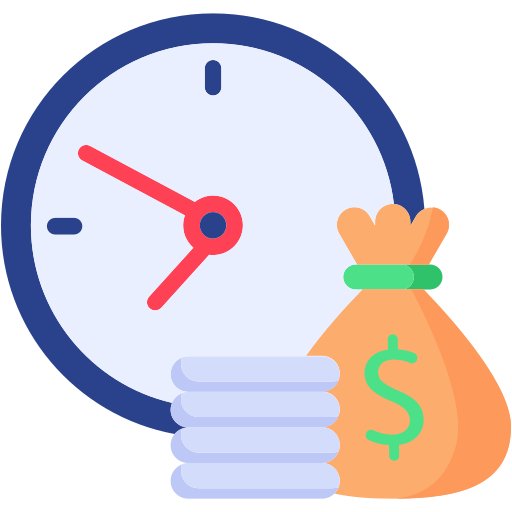
Inspection Time
One of the main reasons for adopting drones for solar panel inspections is reduction in maintenance costs. Typically, inspections of large solar farms are done by a ground team who inspect each panel by hand. This method can take days or weeks depending on the size of the farm and it results in a large amount of man hours which significantly increases costs. Drones are proven to reduce inspection time by up to 70%.

Historical Data
Keeping records of previous inspections is useful for figuring out the causes behind panel faults. In some cases, issues with solar cells do not justify the replacement of a panel, but it is essential to keep track of them to prevent major failures. It is also beneficial to perform an aerial inspection after completing installation of new panels to use the data as a baseline for future inspections.
PV SYSTEM INSPECTION DELIVERABLES
What You'll Receive

An Interactive color-coded map of the PV system with every anomaly geo-referenced
Estimated annual impact of lost revenue if anomalies stayed unresolved
Estimated annual impact in kWh
An exportable CSV, KML, and SHP report file for office and field use
Number of anomalies and modules affected
Estimated affected DC
An exportable PDF report document for each plant inspection containing all analytics, findings tables, and image associated with each anomaly
An exportable CSV, KML, and SHP report file for office and field use
Our Inspections Detect
Steps to Achieving Maximum Energy Production
Step 1 - Contact
We’ll answer any questions you may have and share all the details of what to expect, from the equipment we use, types of data we collect, and deliverables we provide.
Step 2 - Choose a Package Level
You’ll compare and choose the right package level for your needs and we’ll be there every step of the way.
Step 3 - Proposal
Provide us with general information of your PV system including site name, size, and mounting type to receive a free same day quote tailored specifically for your project.
Step 4 - Aerial Thermography Inspection
Using our best-in-class drone technology, our experienced pilots will conduct the aerial inspection.
Step 5 -Recieve an In-depth Report
Discover the located fault types, number of modules affected, estimated affected DC, estimated annual loss in revenue, and more.
Step 6 - Deploy Maintenance Team
Using a site map and geo-referenced photos, your O&M team will be able to easily locate and remediate all issues.
Why SUADRON !!!
What Makes Us Qualified
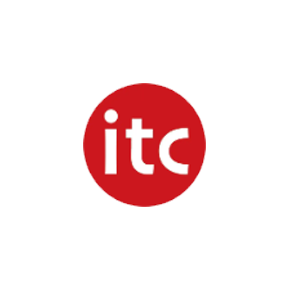
sUAS Level 1 Thermographer
INFRARED TRAINING CENTER The ITC certification is the gold-standard qualification within the thermography industry. Extensive knowledge of infrared science, cameras, and post processing software is taught by the leading infrared drone pilots across the nation.

Luftfahrt-Bundesamtes
The higher federal authority within the portfolio of the Federal Ministry for Digital Affairs and Transport (BMDV), ensures the safety of a flight long before it begins. By performing more than 100 admission, approval and supervisory functions .
General Question
Still have concerns about using drone in solar farm inspection, here is the most frequent asked question regarding this use case.
Drone inspections cost less than manual inspections
Inspection time is 70% faster
Improves preventive maintenance by locating the tracking faults over time
Reports display annual financial loss if anomalies stay unresolved
No plant downtime required
Actionable data for warranty claims
Aerial inspections can identify 100% of faults and identify the type of fault with 99% accuracy. Compared to manual inspections, drones have a much lower inspection time and provide more accurate data. Operations and maintenance teams can also effortlessly identify the location of anomalies with our detailed maps of the solar plant.
Yes. Warranty inspections usually require a thorough review of every module within the solar plant. Our comprehensive aerial inspections quickly and accurately identify warrantable issues and deliver a detailed, actionable report that can be used to submit a warranty claim.
When aerial inspections are performed instead of manual dc inspections, technicians spend less time in the field accessing combiner boxes, inverters, and modules. Drone thermal data can pinpoint where anomalies occur resulting in a more efficient workload for technicians as manual testing is only performed on the impaired areas of the PV system.
In just one solar farm inspection, a large scale solar maintenance service provider had saved 778 man-hours from switching to aerial inspections.
The length of time for an inspection depends on the size of the site. Drones are the quickest and most efficient way of inspecting PV systems and can accomplish what would take manual IV curve testing 1 day in 1 hour. From our data, drones can cover anywhere between 10-50MW in a single day.
7-10 business days.
No. Manual inspections of solar plants can require scheduled downtime which results in lost revenue. With aerial inspections, drones are able to perform the inspection without the need to shut down the solar plant.
Yes. Our comprehensive solar inspections comply with the IEC TS 62446-3 thermography standards set by the International Electrotechnical Commission, the world’s leading organization that publishes standards for all electronic related technologies.